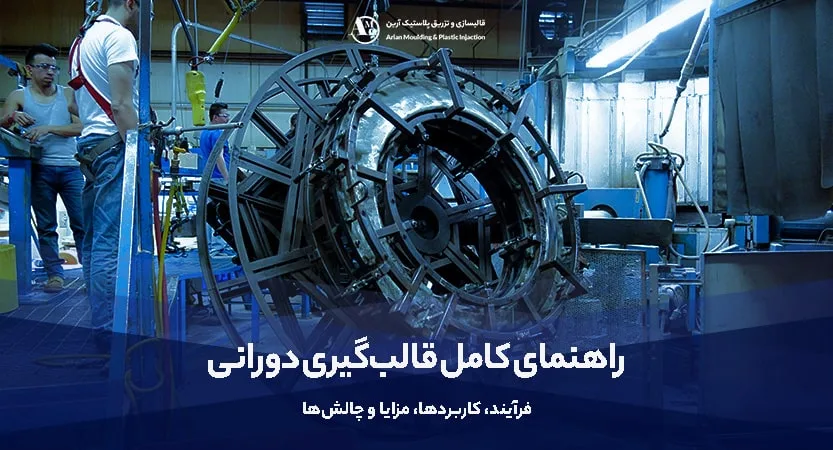
راهنمای کامل قالبگیری دورانی: فرآیند، کاربردها، مزایا و چالشها | قالبسازی آرین
مقدمه
قالبگیری دورانی یا روتومولدینگ یکی از روشهای پرکاربرد برای تولید قطعات پلاستیکی است که در صنایع مختلف استفاده میشود.
این فرآیند به خاطر قابلیت تولید قطعات بزرگ و شکلهای پیچیده، همچنین هزینه نسبتاً پایین، محبوبیت زیادی پیدا کرده است.
در این مقاله، ما به بررسی جامع فرآیند قالبگیری دورانی میپردازیم.
مزایا، چالشها، مواد مورد استفاده و کاربردهای گسترده این روش را به طور کامل تحلیل خواهیم کرد.
فرآیند قالبگیری دورانی چیست؟
قالبگیری دورانی روشی برای تولید قطعات پلاستیکی است که از مواد پودری و حرارتدهی بهره میبرد.
این فرآیند به ما امکان تولید قطعات با ضخامتهای مختلف و ابعاد بزرگ را میدهد.
در این روش، قالبی دوار به کار میرود که با حرارت دادن، پودر پلاستیک ذوب شده و به طور یکنواخت در قالب پخش میشود.
مراحل فرآیند قالبگیری دورانی
- پر کردن قالب با مواد پودری:
در مرحله اول، پودر پلاستیکی مانند پلیاتیلن یا پلیپروپیلن را در داخل قالب میریزند. محاسبه دقیق این مواد پودری ضروری است تا قطعه نهایی از نظر ضخامت و وزن به درستی تطابق داشته باشد.
. - حرارتدهی و چرخش قالب:
قالب در دمای بالا قرار میگیرد و بهطور مداوم حول دو محور عمود بر هم میچرخد. این چرخشها باعث میشود که پودر پلاستیک بهطور یکنواخت روی سطح داخلی قالب پخش شود.
. - سرد کردن قالب:
پس از شکلگیری قطعه، قالب به تدریج سرد میشود تا پلاستیک جامد و قطعه به شکل نهایی خود برسد.
. - خروج قطعه از قالب:
پس از سرد شدن کامل، قالب باز میشود و قطعه نهایی به آرامی از آن خارج میشود.
مواد مورد استفاده در قالبگیری دورانی
در قالبگیری دورانی، از انواع مختلف مواد ترموپلاستیک استفاده میشود. انتخاب ماده مناسب بسته به نیاز و خصوصیات قطعه نهایی انجام میشود.
پلیاتیلن، پلیپروپیلن، پلیوینیل کلراید (PVC) و نایلون از جمله مواد رایج در این روش هستند.
هر یک از این مواد ویژگیها و مزایای خاص خود را دارند که آنها را برای کاربردهای مختلف مناسب میسازد.
رایجترین مواد مورد استفاده
- پلیاتیلن (PE):
به دلیل قیمت مناسب، مقاومت شیمیایی و دوام بالا، بیشترین کاربرد را در قالبگیری دورانی دارد.
انواع مختلف پلیاتیلن شامل چگالی کم (LDPE)، چگالی متوسط (MDPE)، چگالی بالا (HDPE)، شبکهای (XLPE) و کم چگالی خطی (LLDPE) هستند.
هر یک از انواع این مواد ویژگیهای خاص خود را دارند که برای کاربردهای مختلف مناسب است.
. - پلیپروپیلن (PP) :
به دلیل مقاومت بالا در برابر حرارت و مواد شیمیایی، انتخاب مناسبی برای تولید قطعات با استحکام بالا است. این ماده به دلیل ویژگیهای مکانیکی قوی، در صنایع مختلف از جمله خودروسازی و تولید تجهیزات صنعتی کاربرد دارد.
. - نایلون :
به دلیل مقاومت بالا در برابر سایش و حرارت، گزینهای ایدهآل برای تولید قطعات در صنایع خودروسازی و مکانیکی است.
ویژگیهای ممتاز این ماده، آن را به انتخابی مناسب برای کاربردهای صنعتی با شرایط محیطی سخت تبدیل کرده است.
. - پلیوینیل کلراید (PVC) :
به دلیل انعطافپذیری بالا و مقاومت مناسب، برای تولید قطعاتی مانند لولهها و تجهیزات پزشکی بسیار مناسب است.
این ویژگیها باعث میشود که PVC گزینهای مطلوب برای کاربردهایی باشد که نیاز به تطبیقپذیری و دوام دارد.
از دیگر موادی که در فرآیند قالبگیری دورانی مورد استفاده قرار میگیرند، میتوان به موارد زیر اشاره کرد:
- EVA کو- پلیمر (EVA)
- پلی کربنات (PC)
مزایای قالبگیری دورانی
فرآیند قالبگیری دورانی به دلیل ویژگیهای منحصربهفرد خود در تولید قطعات پلاستیکی بزرگ و پیچیده، محبوبیت زیادی پیدا کرده است.
مزایای اصلی این روش به شرح زیر است:
- تولید قطعات بزرگ و پیچیده:
یکی از مزایای مهم قالبگیری دورانی، امکان تولید قطعات بسیار بزرگ و پیچیده با یکنواختی ضخامت و بدون درز است.
. - هزینه تولید پایین:
در مقایسه با دیگر روشهای تولید پلاستیک، قالبگیری دورانی نیاز به قالبهای پیچیده ندارد که این امر باعث کاهش هزینه تولید میشود.
. - انعطافپذیری در طراحی:
این روش به تولیدکنندگان اجازه میدهد تا قطعات با اشکال پیچیده و خاص تولید کنند.
. - بدون درز بودن قطعات:
قالبگیری دورانی این امکان را فراهم میکند که قطعات بدون درز و یکپارچه تولید شوند که به افزایش استحکام و مقاومت آنها کمک میکند.
چالشهای قالبگیری دورانی
هر فرآیند تولیدی با چالشهایی روبهرو است و قالبگیری دورانی نیز از این قاعده مستثنی نیست.
در ادامه به برخی از چالشهای اصلی این روش اشاره میکنیم:
- زمان تولید طولانی:
یکی از بزرگترین چالشهای قالبگیری دورانی، زمان طولانی مورد نیاز برای تکمیل هر چرخه تولید است. این امر به دلیل نیاز به سرد کردن قالب پس از هر چرخه است.
. - محدودیت در مواد قابل استفاده:
در مقایسه با دیگر روشهای قالبگیری پلاستیک، قالبگیری دورانی به مواد بیشتری وابسته است.
. - دقت پایینتر در تولید قطعات کوچک:
این روش برای تولید قطعات بزرگ ایدهآل است، اما برای تولید قطعات کوچک و دقیق دقت لازم را ندارد.
کاربردهای قالبگیری دورانی
قالبگیری دورانی به دلیل توانایی تولید قطعات با اندازههای بزرگ و طراحیهای پیچیده، در صنایع متعددی کاربرد دارد.
از جمله کاربردهای مهم این فرآیند میتوان به موارد زیر اشاره کرد:
- مخازن ذخیرهسازی:
این روش برای تولید مخازن ذخیرهسازی آب، سوخت و مواد شیمیایی بهکار میرود. مخازن بزرگ و بدون درز که توسط این روش تولید میشوند، از استحکام بالایی برخوردارند.
. - اسباببازیها:
بسیاری از اسباببازیهای پلاستیکی مانند توپهای بزرگ و تابهای پارک کودکان با استفاده از قالبگیری دورانی تولید میشوند.
. - قطعات صنعتی و خودروسازی:
در صنایع خودروسازی و تجهیزات صنعتی نیز از این روش برای تولید قطعات خاص و بزرگ استفاده میشود.
. - قطعات پزشکی:
قالبگیری دورانی در تولید تجهیزات پزشکی که نیاز به طراحیهای پیچیده دارند، مانند تجهیزات جراحی و مخازن پزشکی بهکار میرود.
نوآوریها و پیشرفتهای جدید در قالبگیری دورانی
در سالهای اخیر، پیشرفتهای جدیدی در حوزه قالبگیری دورانی رخ داده است که این فرآیند را بهبود بخشیده و قابلیتهای آن را افزایش داده است:
- استفاده از مواد چندلایه:
استفاده از پلیمرهای چندلایه در فرآیند قالبگیری دورانی امکان تولید قطعات با خواص مکانیکی و شیمیایی بهتر را فراهم میآورد.
. - اتوماسیون فرآیند:
با استفاده از تکنولوژیهای رباتیک و سیستمهای کنترل اتوماتیک، دقت و سرعت فرآیند بهبود یافته است.
. - بهبود سیستمهای خنککننده:
نوآوری در سیستمهای خنککننده قالب، باعث کاهش زمان تولید و افزایش کیفیت قطعات شده است.
نتیجهگیری
قالبگیری دورانی به عنوان یکی از مؤثرترین و مقرونبهصرفهترین روشهای تولید قطعات پلاستیکی بزرگ و پیچیده شناخته میشود.
این فرآیند به دلیل مزایایی مانند تولید قطعات بدون درز، کاهش هزینه تولید و انعطافپذیری در طراحی، همچنان در صنایع مختلف محبوب است.
با این حال، چالشهایی نظیر زمان تولید طولانی و محدودیت در مواد نیز باید مد نظر قرار گیرند.
پیشرفتهای تکنولوژیکی اخیر، از جمله استفاده از مواد چندلایه و اتوماسیون، آینده این فرآیند را روشنتر کرده است.
دیدگاهتان را بنویسید